Путешествие за краем карты: создание цифровых двойников российских заводов Bosch
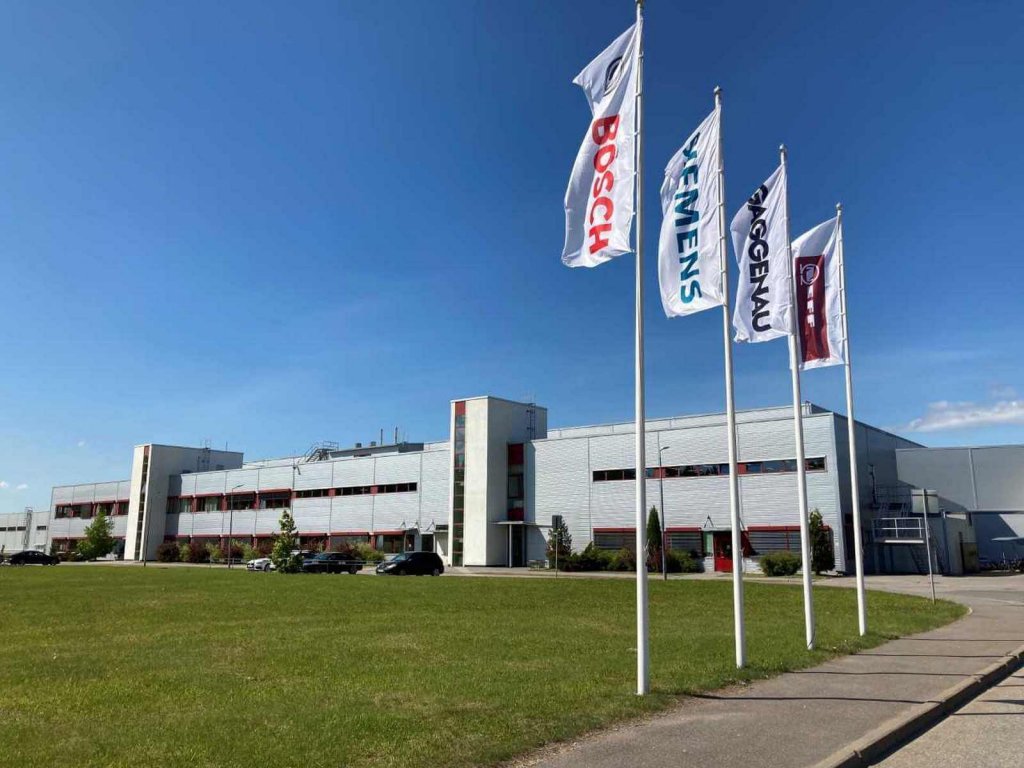
Понятие цифрового двойника в мире трактуется очень широко, и единого понимания этого явления пока нет ни в мире, ни в России, где на данный момент написан только предварительный стандарт. Компаниям и предприятиям приходится двигаться на ощупь, практически без ориентира, разрабатывая уникальные концепты виртуальных моделей только с помощью собственного опыта и знаний. Прототипы постепенно формируют базу для создания общих стандартов цифровых двойников промышленного предприятия и служат примером для производственных площадок из разных сфер, двигающихся по направлению к Индустрии 4.0. Марина Ершова, руководитель департамента технологий и инноваций «БСХ Бытовые Приборы», дочерней компании входящего в Группу Bosch производителя бытовой техники, рассказывает об опыте создания цифровых двойников двух российских фабрик компании.
Поиск новых методов повышения эффективности
Одна из долгосрочных целей глобального концерна BSH — завершение цифровой трансформации компании к 2025 году. Реализация этой цели в Европе началась в 2015 году. Примерно к 2018 году все предприятия бренда в разных странах получили возможность пользоваться накопленным европейскими коллегами опытом в качестве базовой дорожной карты цифровизации своих площадок.
В России команды фабрик компании «БСХ Бытовые Приборы», производящих бытовую технику: стиральные машины и холодильники — под маркой Bosch, не рассматривают цифровую трансформацию как дань модным трендам и процесс ради процесса. Результатом видятся новые способы повышения эффективности и гибкости, возможности развития взаимодействия с клиентами, поставщиками и другими заинтересованными сторонами. Поиск этих путей ведется постоянно и входит в ДНК концерна.
В 2018 году для команды, управляющей российскими производственными площадками, одним из возможных направлений повышения эффективности стала роботизация. Хронологически этот момент совпал с периодом, когда накопленные европейскими коллегами знания в области цифровых двойников достигли уровня, позволившего описать и транслировать реальный опыт создания виртуальных моделей.
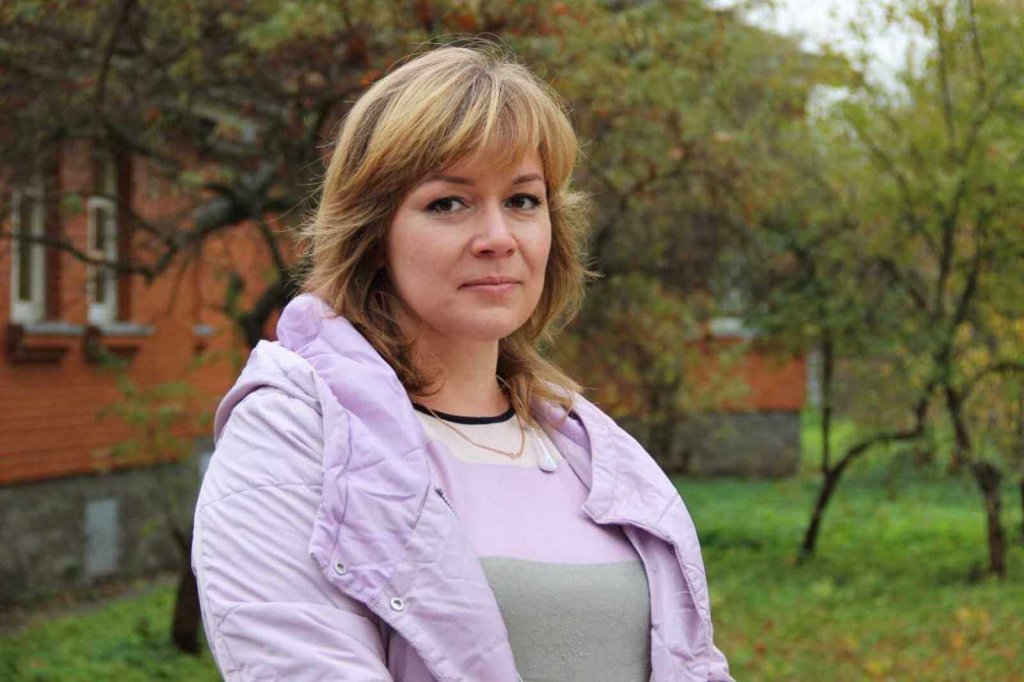
Универсальное средство для тестирования новых идей
Благодаря отсутствию общих стандартов, в каждой компании есть свое уникальное понимание цифрового двойника. Это может быть комплексное или точечное решение — например, функциональная модель целого предприятия, в которой реализован обмен данными в реальном времени с физическим прототипом, или простое виртуальное описание рабочего места.
Широкая трактовка понятия цифрового двойника позволяет использовать модели для разных целей: оптимизации взаимодействия с клиентами и поставщиками, сокращения затрат и потребления энергоресурсов, снижения воздействия на экологию, повышения эффективности оборудования, оптимизации числа рабочих мест.
Команду, занятую автоматизацией процессов на предприятиях Bosch в России, заинтересовала возможность моделирования рабочих процессов и тестирования изменений в виртуальной реальности. Метод позволяет оценить эффективность рабочего места в условиях замены ручного труда роботизированным.
Принципиальная сложность оценки новых концепций и оборудования в условиях любого производственного предприятия заключается в необходимости значительных инвестиций в каждый пилотный проект. Создание цифрового двойника — универсальное решение, позволяющее оптимизировать затраты. Инвестиции в создание модели несопоставимы с затратами на приобретение промышленного робота, оборудование экспериментального рабочего места, пуско-наладочные работы.
Дополнительным стимулом к поиску новых, нестандартных решений, послужила пандемия, когда выполнение планов по модернизации одной из производственных площадок Bosch оказалось под угрозой. Подключение иностранных специалистов дистанционно, с помощью средств VR, для обсуждения технических деталей пусконаладочных работ на российском предприятии стало прецедентом в истории производства Bosch. В результате процесс, который до пандемии был исключительно физическим, удалось полностью перенести в виртуальную реальность. Изучение полученного опыта показало, что запуск поточной линий с применением цифровой модели делает проект менее затратными и более оперативным. Этот опыт стал одним из факторов, привлекших внимание к потенциалу цифровых двойников.
Средства для создания виртуальных моделей
Для создания виртуальной модели роботизированного рабочего места в компании использовали программное обеспечение Process Simulate из пакета Tecnоmаtix.
Решение разработано для моделирования и оптимизации производственных систем и процессов. На выбор инструмента повлияло и то, что PLM-системой на предприятиях концерна является Teamcenter, созданное тем же разработчиком (Siemens). Благодаря этому в программных средствах предусмотрена возможность быстрого обмена данными — например, можно загрузить в Process Simulate 3D-модель холодильника или производственного помещения из Teamcenter.
Программное обеспечение позволяет менять различные параметры модели. Есть возможность отправить приглашение на тестовую сессию другим участникам при условии, что у них установлено такое же программное обеспечение. Приняв приглашение, получатель виртуально «оказывается» в том же месте, где находится отправитель. Подключиться к встрече можно с помощью гарнитуры VR, однако в программе реализована возможность транслировать изображение в гарнитуре на экран компьютера. Это дает возможность принимать участие в обсуждениях специалистам разных направлений, от инженеров до руководителей производства, без дополнительного технического оснащения.
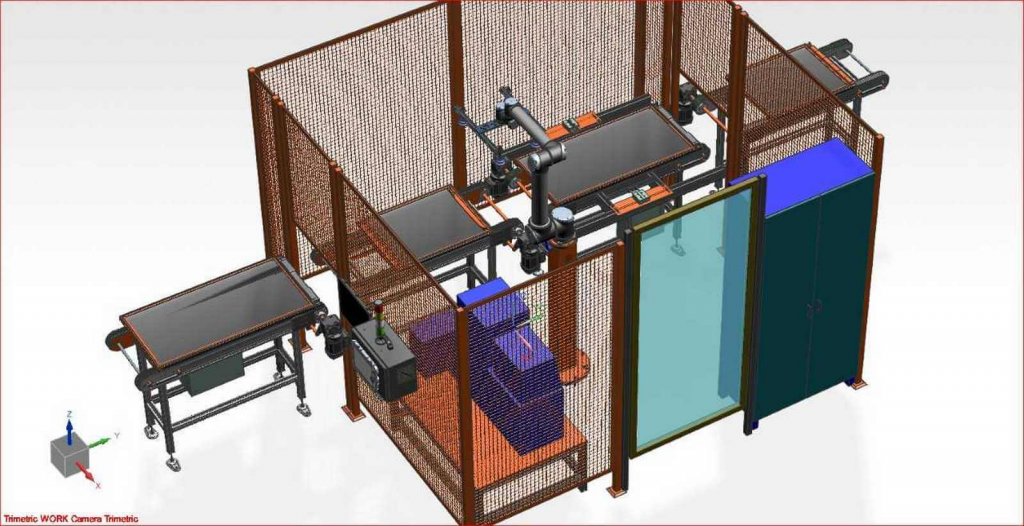
Выбор уровня цифрового двойника в соответствии с задачей
Полученный опыт работы с программным обеспечением убедил команду в возможности создания существующими средствами цифровых двойников рабочих мест и дополнения их моделями промышленных роботов для последующего тестирования ряда параметров.
Сложившаяся практика моделирования показывает, что уровень модели во многом зависит от сферы деятельности предприятия и поставленных задач. В добывающей отрасли помимо виртуальной модели оборудования требуется моделирование физико-химических процессов. Это обусловлено задачей — например, оценки запасов месторождения или проектирования газопровода. Задача может быть решена с применением модели только в том случае, если она включает характеристики оборудования и характеристики среды, например нефти (жидкости) или природного газа.
Потенциально такая сложная модель может быть интересна — для поиска точек роста эффективности или других целей — промышленному предприятию любой отрасли.
Поводом к поиску более простых решений для оценки эффекта от роботизации был и ряд ограничений, в условиях которых работала команда. Одним из них было и остается лимитированное финансирование, невозможность выделения рабочей группы из сотрудников предприятий, сконцентрированных на проекте, и привлечения дополнительных специалистов. Деятельность по проекту осуществляется в рамках рабочего времени штатными сотрудниками предприятий. Еще одно ограничение заключается в невозможности останавливать производство и модернизировать оборудование, устанавливая датчики для создания модели, за исключением особых случаев.
Выход был найден в использовании распределенных точечных решений. Команда создает модели для отдельных рабочих мест в рамках их запланированной модернизации.
Для оценки эффекта от роботизации команда создает цифрового двойника рабочего места и дополняет его 3D-моделью промышленного робота. Затем модели загружаются в программную среду и объединяются. Это дает возможность проанализировать различные физические свойства и пространственные характеристики модернизированного рабочего места. В частности, проводится оценка изменений эргономики рабочего места, необходимого для беспрепятственных операций робота с соблюдением норм охраны труда.
В процессе работы у группы сформировались предварительные стандарты модели, уровня которой достаточно для выполнения существующей задачи. В частности, удалось выяснить, что детальная отрисовка участка производственной линии не требуется.
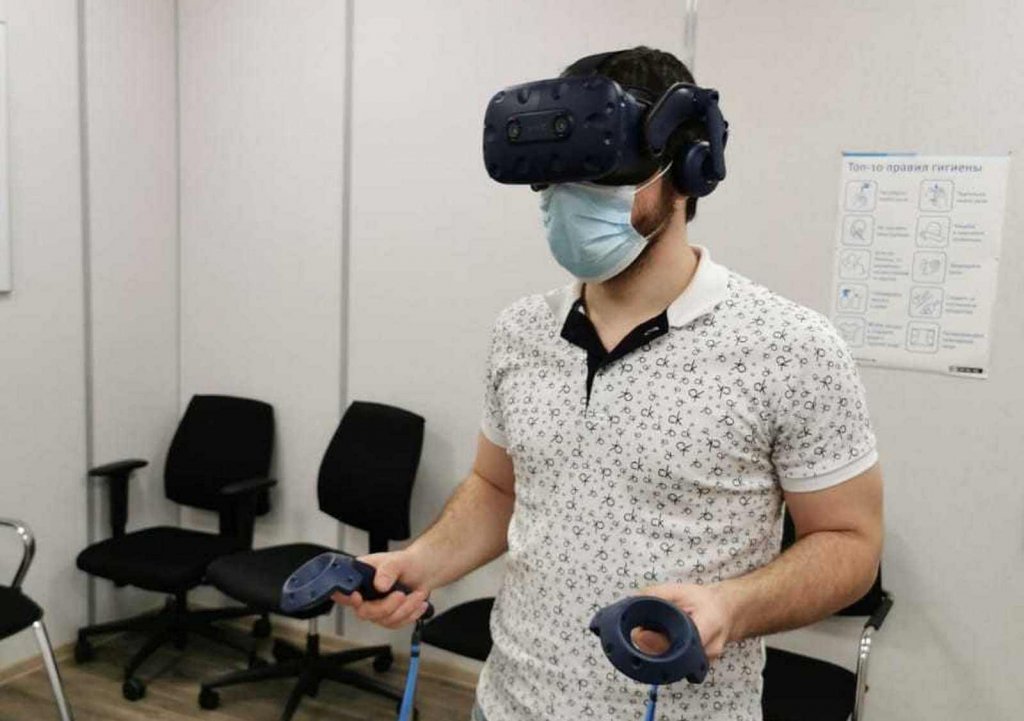
Выбор методики для создания моделей
Установив для себя уровень модели, группа пришла к решению использовать метод 3D-сканирования для создания двойника. Источником решения послужил уже существующий опыт европейских площадок концерна.
Решение оказалось оптимальным по ряду параметров. 3D-сканирование - достаточно распространенная услуга с доступной стоимостью. Методика применяется в разных областях — от кинопроизводства до строительства. С помощью 3D-сканера можно оперативно, в течение одного рабочего дня, получить необходимые для построения модели данные. Средняя стоимость услуг подрядчика в объеме, достаточном для создания 3D-модели рабочего места, составляет 30 тысяч рублей.
Устройство сканирует до нескольких миллионов точек в секунду. Сканер описывает объект с помощью облака точек, обладающих координатами в трехмерном пространстве. Облако точек соответствует поверхностям объекта. Модель позволяет определить границы объекта и наружную фактуру. Дополнив эти данные моделью робота, эксперты оценивают параметры виртуального рабочего места, являющегося двойником реального прототипа.
Перспектива использования опыта
Первоначально процедура была проведена для двух пилотных участков на разных предприятиях — по производству стиральных машин и холодильников. Успешный опыт позволил задуматься о возможных путях развития направления цифровых двойников и вариантов практического применения в условиях промышленного предприятия.
Одним из дальнейших путей развития видится дополнение цифрового двойника предприятия цифровыми двойниками отдельных участков и целых поточных линий, a также описательной частью по каждому объекту.
Teamcenter — это среда, которой пользуются конструкторы, разработчики и дизайнеры, работающие над новыми продуктами, PLM-cистема для управления жизненным циклом продукта и обеспечивает доступ к информации об изделиях и процессах в распределенной среде. С помощью Teamcenter можно управлять моделями продуктов, созданными средствами CAD, объединять данные об электронных системах и программном обеспечении продукта, устанавливать взаимосвязь между конструкторскими и расчетными данными.
Получив доступ к цифровому двойнику производства, инженеры-технологи смогут анализировать путь изделия, моделируя его с помощью цифровых ассистентов. Использование виртуальной модели даст возможность детально проработать весь технологический процесс сборки. Созданное решение станет комплексной рабочей средой для всех специалистов, причастных к производству продукта, — инженеров, конструкторов и технологов.
Однако, чтобы такая возможность появилась, необходимо реализовать комплексный проект, в который помимо моделей войдут описания всей структуры процессов, ресурсов, необходимых для создания продукта, библиотека настраиваемых параметров оборудования, описание оснастки и другая релевантная документация. Фактически это равноценно созданию единой базы знаний по продукту и процессу его создания, которая станет основой для моделирования продукта в виртуальной среде.
Поскольку все программные средства интегрированы между собой, теоретически создание продукта и его тестирование в динамике возможно. В то же время для практической реализации такой комплексной среды необходимо провести работу, оцифровав всю документацию и сделав описания всех наработок, созданных на предприятии за 10 лет.
Аналогичная работа уже активно идет на уровне всего концерна, и в ближайшее время будет готов интерфейс между виртуальной средой разработки и MES-системой для обмена данными с программируемыми контроллерами, управляющими оборудованием. Это даст возможность управлять настройками физического объекта посредством изменений параметров его цифрового двойника, исключив влияние человеческого фактора на эффективность производства.
Дальнейшие этапы развития цифрового двойника предприятия
Команда, работающая над проектом, провела первоначальную оценку времени и инвестиций, необходимых для создания полноценной цифровой модели предприятия высокого уровня. Для этого понадобилось разделить проект на этапы, оценить уровень затрат по каждому и расставить их в порядке приоритетности и целесообразности выполнения на данном этапе развития предприятия.
Полностью функциональная цифровая модель предприятия подразумевает непрерывный обмен данными между виртуальной и физической средой. Это означает, что все изменения в реальном оборудовании и процессах должны отражаться в модели — и наоборот. Благодаря этой особенности время работы над двойником фактически равно периоду существования предприятия.
Несмотря на то, что финальной точки у проекта нет, команда выделила в нем ряд этапов, длительность которых можно рассчитать. Первоочередной задачей специалисты BSH считают моделирование всех рабочих мест и создание описания для каждого процесса. Вторым этапом должно стать создание цифровой библиотеки параметров.
Чтобы завершить первый этап на двух предприятиях, команде в текущем составе, работающей по проекту без отрыва от основных обязанностей, потребуется от полугода до года. Специально собранная для проекта команда из 10 человек, в которую входили бы специалисты, обладающие опытом создания двойников методом 3D-сканирования, знающие производство и программное обеспечение, проделала бы ту же работу приблизительно за два месяца.
Но сроки могут меняться в зависимости от стадии цифровой трансформации, на которой находится предприятие. Не секрет, что в целом для российской промышленности характерен низкий уровень технологического оснащения. На многих предприятиях нет 3D-моделей оборудования и нет технологий, которые можно было бы использовать при создании цифрового двойника.
Экономический эффект
Проект по созданию цифровых двойников предприятий Bosch в России находится на начальном этапе, поэтому провести оценку экономического эффекта от создания модели высокого уровня пока невозможно. Однако команда уже сейчас обладает данными по эффекту от «программы минимум» — создания виртуальной модели рабочего места для оценки преимуществ роботизации.
Использование цифрового двойника в сочетании с опытом пусконаладочных работ в условиях пандемии позволяет провести интеграцию робота самостоятельно, исключив затраты на работу специалистов производителя оборудования и интегратора. С учетом низкой стоимости ручного труда и, как следствие, низкого уровня роботизации на российских предприятиях, экономия 50% стоимости делает проект по автоматизации большинства рабочих мест экономически обоснованным.
Фото: Bosch
мероприятий